
Intelligent Products
Intelligent Products improve the employee experience in manufacturing
Manufacturers have a people problem. There aren’t enough of them. And oftentimes they don’t have the right mix of skills and experience.
In fact, skills shortages will hit 90% of industrial companies by 2025, imposing significant constraints on production capacity, according to the World Economic Forum.
So, what’s driving this global labor shortage in manufacturing? There are a few factors.
- Older, more experienced workers are retiring.
- Younger workers don’t have the needed skills.
- People are choosing other industries that offer better jobs: more meaningful work and higher paid roles in safer, more comfortable conditions.
- Manufacturers saw over 5% reduction in their workforce due to the pandemic.
Many modern manufacturers are addressing this people problem with intelligent technology, helping provide a vision and direction for meaningful work, plus the tools, support, and workplace safety infrastructure that attracts new talent.

Intelligent Products have enormous potential to give employees a much better experience on production lines and shop floors, in administrative offices and supply chains. These solutions incorporate artificial intelligence (AI) and/or machine learning (ML) in support of smart factories, and they put manufacturing data to work in making people’s jobs better.
“The truth is that AI doesn’t replace good professionals …. Instead, it pulls low-level workers up to mid-level workers, improving the quality of work for those who are not already highly skilled,” says Igor Bogachev, co-founder of CloEE, an IoT SaaS.
Let’s get into some specifics. How, exactly, can Intelligent Products create a better experience for manufacturing employees?
Want to hire (and keep) more workers?
Automate repetitive tasks.
When the actual work that manufacturing employees perform is tedious or limited, it can translate to less appealing roles. By digitizing those undesirable tasks using built-in intelligence, manufacturers can hire and keep workers more easily.
In technology-driven facilities, an upskilled technologist can perform a variety of operations, instead of just one. They might also handle quality checks and know how and why to position machine-vision cameras for automated visual inspections. A more efficient and data-driven workforce like this can fulfill more comprehensive roles and earn higher wages. And that leads to higher employee satisfaction and retention.
Examples of intelligent automation:
- Deploy autonomous guided vehicles (AGVs), which can move parts between processing stations without human intervention.
- Add intelligence to threshold monitoring so that when levels go into the red (for example, when they reach 90% of the maximum temperature or pressure), the process is automatically adjusted to compensate, rather than requiring manual adjustment.

Want to keep employees safer?
Deploy predictive maintenance and monitoring.
Malfunctioning equipment and sudden hazards can lead to accidents, injuries, and unplanned downtime. Analyzing historical performance and maintenance data, plus real-time updates from safety sensors, can highlight potential problems before they happen.
Examples of intelligent safety improvements:
- Employ Internet of Things (IoT) and smart sensors to set up a digital perimeter around hazardous processes and reduce the chance of injury.
- Use AI/ML and computer vision to proactively find security or safety concerns before they cause an incident.
Concerned about employee burnout?
Generate insights into workload, utilization, and well-being.
Chronic stress and exhaustion can lead to increased turnover and absenteeism in manufacturing workplaces. Burnout may be caused by heavy workloads, tight deadlines, lack of autonomy, and inflexible schedules, among other factors.
In addition to automation efforts mentioned earlier, Intelligent Products can come into play by balancing employee responsibilities, informing shift planning, and predicting demand fluctuations.
Examples of intelligent worker insights:
- An AI algorithm could analyze data from scheduling software, production equipment, and employee surveys to pinpoint the best utilization levels and generate assignments automatically.
- Employee burnout could be predicted by monitoring employee surveys, performance metrics, and absenteeism rates, and feedback and recommendations could be generated to help adjust and prevent stress.
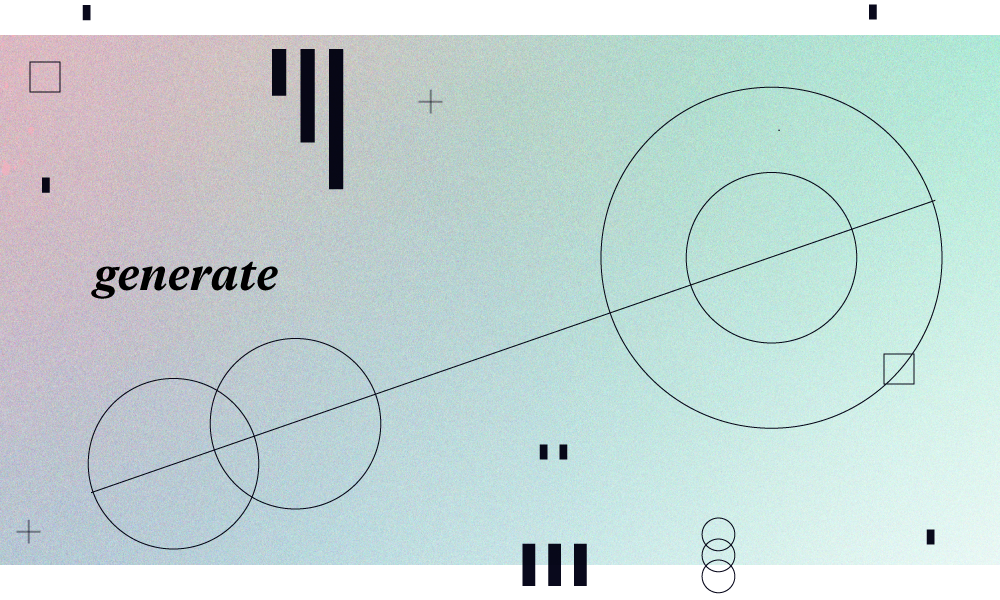
Want to train people faster and improve performance?
Use intelligent assistants for recommendations and feedback.
Since skill gaps are particularly an issue for in-demand entry level positions, Intelligent Products such as chatbots and responsive training simulators can be valuable for onboarding new employees, providing orientation, and assessing progress. These AI solutions can also help more skilled workers with operational technology (OT), supplying troubleshooting options and efficiency recommendations on the spot.
Examples of intelligent training:
- An AI system can monitor sensors to detect when a product falls outside certain quality parameters and make suggestions for how a human operator can correct the problem.
- Collaborative robots can show employees how to execute a task, assess their performance, and suggest improvements.
How can you get employees engaged and boost satisfaction?
Enable innovation and new business models.
This is where Intelligent Products get exciting. AI can help drive creative ideas for perfecting production, especially around meaningful goals like quality and ecoefficiency. It can support generative product design and find novel uses for waste streams.
Examples of intelligent innovation:
- AI and ML can support high levels of automated customization, allowing products to be tailored to individual buyers without increasing cost.
- Intelligent Products can responsively reduce energy use and analyze sensor data for inefficiencies such as water leaks.
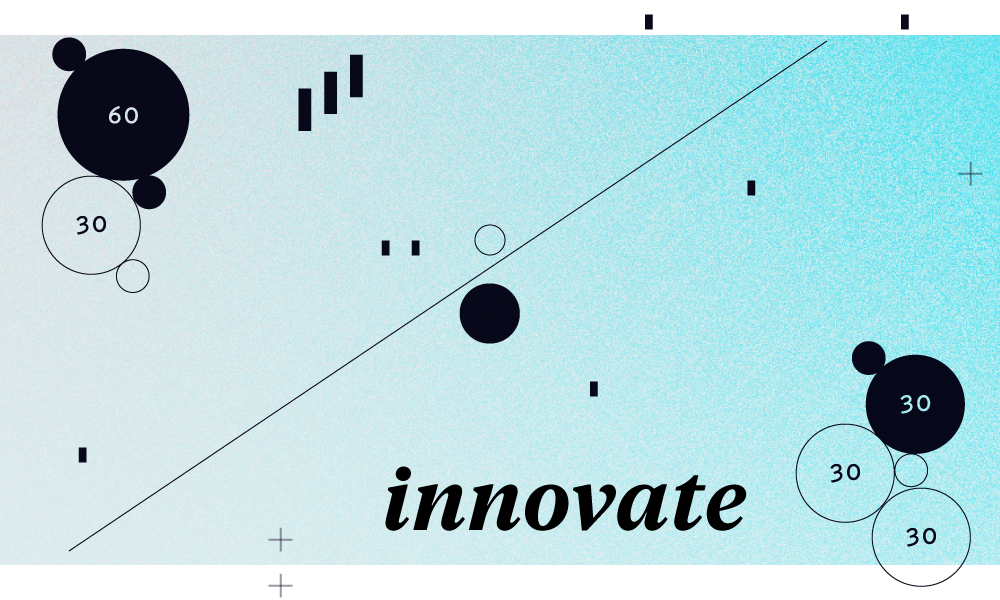
Our work with Just Right Customer Solution (JRCS) is an example of the tremendous potential that Intelligent Products hold for improving employee experience. Originally JRCS approached Slalom Build to incorporate intelligence into their marine navigation hardware to enable smart navigation. The system takes in sensor data and live camera feeds to support decision making and ease the challenges of piloting a ship at sea.
However, through our collaborative engagement with their team, the goal evolved into a larger vision for smart ships that reduce (and may eventually eliminate) the need for human navigation. The JRCS business model is expanding from the shipping companies that buy their hardware to the end customers that need to move containers from one port to another. The sensor data can be analyzed and used to supply even more services to other manufacturers moving goods around the world.
Our full-length JRCS customer story goes into detail on how their team was empowered and challenged by the opportunities presented by Intelligent Products.
The predictions that technology and AI will replace human workers have been turned on their head—economic and demographic pressures are demonstrating just how vital it is to have a skilled, experienced labor force in manufacturing. Forward-thinking companies are turning to Intelligent Products to attract people to jobs that are safer and more rewarding.
For a deeper dive into the benefits of AI/ML for your employees, clients, and business, read our guide to Intelligent Products.